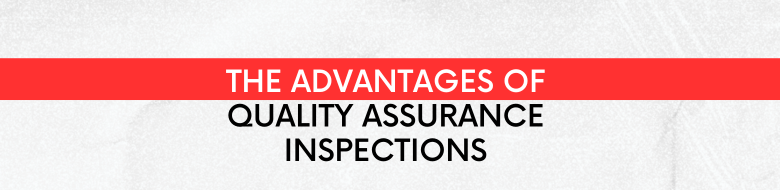
In order to guarantee customer pleasure and meet consumer expectations, quality management is a crucial component.
An efficient, well-organized quality management plan ensures that the standards established for a specific good or service truly serve their intended purpose.
However, what exactly is a quality management plan? What issues require our focus during the planning process? How can the quality management processes be accelerated?
Discover how planning may guarantee delivery within the designated period, achieve the project’s standards, and lower time and rework costs.
A quality management strategy is what?
One of the stages in the development of a project is the quality management plan. It will outline the standards, practises, and tools needed to make it happen. There are three primary sections to the plan:
Planning
It entails setting requirements for standards and quality as well as describing how the project complies with established standards. Parallel to the other project planning stages, this phase should be carried out.
Management
Everything that was suggested during planning must be put into practise through quality management. The auditing and controlling processes that guarantee adherence to the established quality standards will take place at this phase.
Change requests, modifications to the management plan, documentation, and data regarding the effectiveness of the generated work may all come up during this phase.
Control Control, often known as monitoring, is the procedure in charge of keeping the quality consistently at the intended level. Improvements will also emerge during the control phase in an effort to strengthen the procedures already in place by identifying areas where the desired outcomes have not been attained.
What elements require consideration during planning?
Planning should take into account the seven quality management principles outlined in ISO 9001:2015. These are subjects that, if handled properly, will result in the delivery of a project of a high calibre. As follows:
Concentrate on the client
Who is quality for? To pursue quality is to recognise that every project’s goal must be to satisfy the client if it is to succeed. Actually, it ought to be the company’s overall goal. As contentious as it may sound, focusing on the client while keeping quality in mind requires looking within, establishing standardised procedures, regularly training staff members, and engaging in continuous improvement.
Involving others
A committed leadership will increase participation since, after all, a watch only functions properly when all of its cogs are turning in the same direction. This is directly related to the previous argument.
A committed team must comprehend not only the process they are a part of, but also its significance on a larger scale. What effect this process will have on the following processes and how important it is for an excellent delivery.
Process strategy
Understanding the inputs, outputs, and how they will be used in the next stage are the main goals of the process method. Future enhancements will be easier to make if the processes are thoroughly understood and documented. The PDCA process must be emphasised in this context since it encompasses all aspects of participating in plans, task execution, monitoring task completion, and corrective or preventative actions.
Continual Development
Anyone who remains motionless in the fast-paced world of today is already regressing. In addition to attempting to enhance what has already been accomplished, the pursuit of improvement entails preventing the lapse into oblivion of the quality controls put in place at the outset of the project. What is useful today might not be so tomorrow.
Making decisions based on facts
The development of analysis and the gathering of data will result in better decision-making and advancements because decisions cannot be decided solely on speculation. Data from performance indicators will be used to monitor and assess progress. The information will demonstrate whether the business is headed in the right path or whether a change is necessary in order for it to produce the intended results.
Streamline the procedures for quality management
It need continuous monitoring, effective communication among the people involved, well-structured flows, and current documentation to maintain quality. To maintain a history of these processes and to be aware of the project’s status, every action should be documented.
Use process automation, change tasks from being informal to following a flow with defined, standardised actions, giving managers control, to expedite management and ensure that the project is fully documented.
Value for quality management is necessary.
The adage “Better safe than sorry” applies here. Unfortunately, some people continue to undervalue the significance of developing a quality management plan, given that its primary function is to guard against potential missteps that can occur throughout the course of the project.
A well-crafted quality management strategy will not only produce outcomes that adhere to the project’s specifications, but it will also prevent major adjustments that result in rework and, as a result, expenditures for the business. Quality entails putting the needs of the customer first, having dedicated staff, and being a reputable institution in the marketplace.
Take a minute to delve even more deeply into the topic of quality indicators by taking up the quality management courses at LBTC.
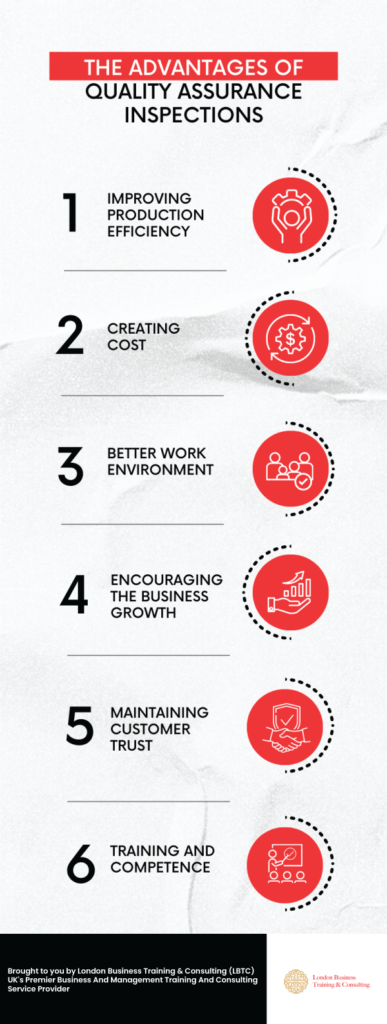
Leave a Reply