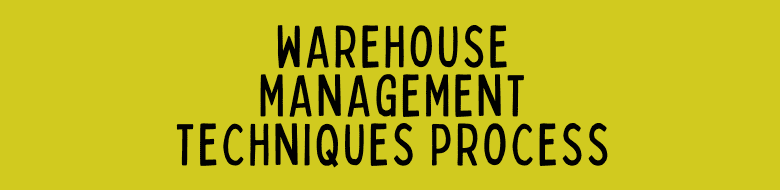
We are here to explain some specifics of increasing warehouse productivity and efficiency, emphasising lowering operational expenses and streamlining your procedures. We provide an overview of valuable strategies that can help you improve customer retention, expedite warehouse operations, and boost your bottom line.
Customer retention and warehouse effectiveness go hand in hand. Your client retention rate will show a decline in warehouse efficiency. Your business’s bottom line will suffer if clients choose a competitor who offers speedier product delivery.
5 Ways to Boost Warehouse Operations and Efficiency
1. Boost Storage in Warehouses
Online shopping is becoming more popular, which increases the demand for suppliers and the requirement to increase inventories. Customers also want greater personalisation and customisation options in the things they buy, according to a 2018 study.
As more SKUs are added to your warehouse, more product varieties equate to more inventory. While warehouse square footage is cheaper than other commercial real estate, expansion is sometimes simple.
Establishing a second fulfilment facility or expanding an existing one can be expensive. We discovered a wide range of estimations. Where you choose to start your new location has a significant impact on the price.
Instead, start by making the most of the available area. Reduce the spacing between aisles as you build storage upstairs to determine if you can add more storage aisles. Making alternating one-way aisles in place of two-way traffic aisles is one technique to do this.
This can significantly increase the effectiveness of stow and pick in addition to allowing you to get more storage out of your warehouse space:
While choosing or storing equipment, equipment handlers have access to the aisle on either side of the aisle.
- reduces the likelihood of equipment hitting one-way traffic
- shorten the distance between each aisle
- enhancing warehouse security by removing the requirement for workers to exit equipment
When Johnson Controls optimised a new facility in 2016, they employed logistics software. The company used the logistics simulation programme to build the most effective warehouse architecture for the new location, which increased picking capacity by 30%.
Storage, efficiency, and performance can all be dramatically improved by carefully planning the layout and flow of your warehouse. Most small enterprises need more funds to invest in pricey warehouse planning tools. However, with a pen, some paper, and some time to take a fresh look at your warehouse, you may maximise its usable area and performance.
2. Provide more pick-up and delivery options for customers
Moving goods downstream to retailers can save warehouse operating costs and lessen the inventory burden.
The inventory responsibility has begun to be transferred to retail outlets by large retailers. For instance, Target disclosed that 15% of its online orders are tagged for in-store pick-up. Allow local pick-up for your clients if you have retail locations that can handle fulfilment.
Consider Amazon if you’re looking for internet merchants without physical sites. Suppliers and merchants can utilise Amazon Fulfilment to sell goods on the marketplace that are kept and delivered by Amazon’s warehouses.
2. Provide more pick-up and delivery options for customers
Moving goods downstream to retailers can save warehouse operating costs and lessen the inventory burden.
The inventory responsibility has begun to be transferred to retail outlets by large retailers. For instance, Target disclosed that 15% of its online orders are tagged for in-store pick-up. Allow local pick-up for your clients if you have retail locations that can handle fulfilment.
Consider Amazon if you’re looking for internet merchants without physical sites. Suppliers and merchants can utilise Amazon Fulfilment to sell goods on the marketplace that are kept and delivered by Amazon’s warehouses.
3. Upgrade Your Warehouse’s Pick and Pack Routes
The time pickers spend between orders and finding items to be selected is one of the significant resources consumers have in warehouses.
According to studies, order picking accounts for about 60% of a warehouse’s labour costs or about 65% of the operational budget for a typical warehouse.
You may significantly lower your overhead expenses by putting a supply chain management system in place. This system keeps track of each product’s details and warehouse location when in use. The system will instruct where products should be placed at your warehouse.
A sound order fulfilment system will also direct pickers along the best path possible. The system will give selectors the best route around the warehouse from product to product based on product characteristics and incoming orders. This significantly decreases the time spent going around and looking for products, which is costly and drains staff time.
4. Update Your Warehouse’s Mobile Technology
Most companies know how technology may boost productivity and expedite order processing. All this adds up to cost savings, but only if you employ the appropriate modern equipment. In the future, 67% of warehouses intend to handle inventory using mobile devices.
That’s a wise investment, too.
When people think about warehouse mobile devices, they typically imagine barcode scanners. However, your staff can also use cell phones and tablets outfitted with a system to get pick orders and the best picking routes. Thanks to WiFi, they can receive the order from anywhere in your warehouse.
5. Establish a procedure for inventory reviews
Even though we may deliver goods to clients more quickly than ever, this has yet to impact how long goods remain in your warehouse. Supply Chain Digest reports that despite the growth in the number of SKUs being replenished daily, businesses are still holding onto more inventory.
Based on an average sales day, the amount of inventory on hand has increased by 8.3% during the previous five years.
Data must be used to review your inventory at this point because having dead merchandise fill your warehouse costs you money.
Utilise metrics to optimise your inventory. Inventory audit: Identify the stock that isn’t moving. Monitoring metrics include:
- Days on average to sell inventory
- The frequency of product inventory turnover
- The return on investment and how it declines with time after purchasing the product
- Products’ gross profit (price minus expenses for production, storage, and sale)
An excessive amount of inventory holding reduces profit margins and costs money. Find a means to sell those items or eliminate them from your stock.
Each warehouse has the potential to enhance efficiency and lower expenses.
The suggestions above have the potential to enhance the efficiency of your warehouse. You can find bottlenecks and ways to increase warehouse efficiency by conducting an audit of your operations. The optimal approach involves implementing a comprehensive warehouse management system and an ongoing assessment of KPIs and performance. As you gradually incorporate these changes, you will observe a continuous reduction in costs and the introduction of innovation into your warehouse operations.
Additionally, considering your recent participation in a warehouse management course, these strategies could align well with your newfound knowledge and further contribute to your warehouse’s success.
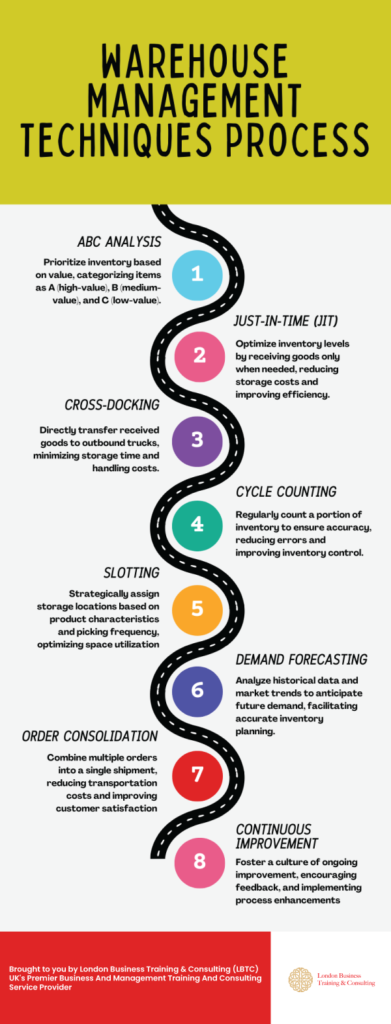
Leave a Reply