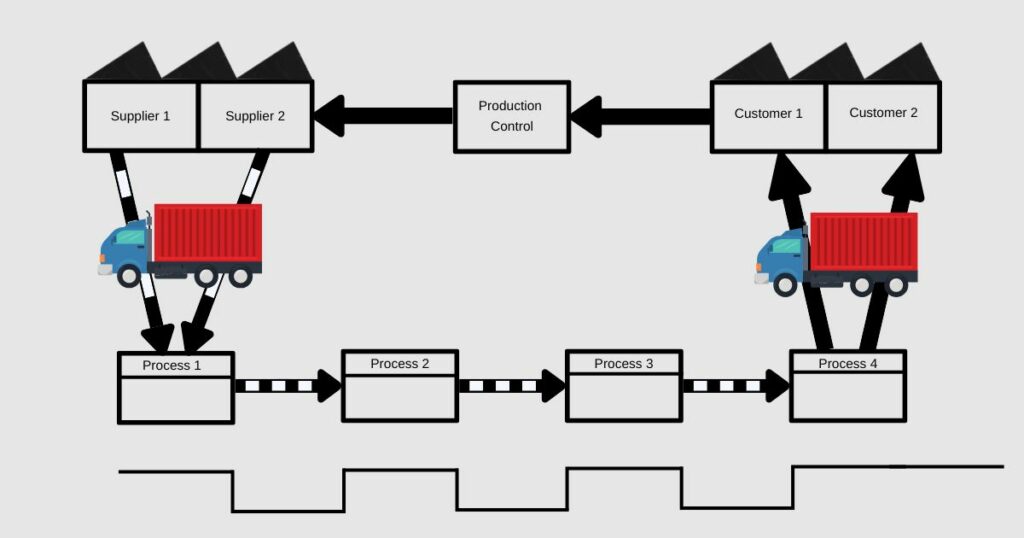
What is Value Stream Mapping?
Value stream mapping, also known as VSM, is a lean management tool used to identify and analyse the state of a product and re-design it to minimise waste. It visually represents the flow of materials, information, and resources involved in this process. VSM helps to identify waste and create opportunities, which allows businesses to increase their work efficiency and productivity and reduce the cost of the operation.
What is VSM’s importance in Business Operations?
The power of VSM is its simplicity and clarity. Hence, it should be included in the tools of all operations teams:
• Improved Visualisation: Even the most complex workflows can be easily broken down into comprehensible visuals by VSM, making it easy for managers to identify the issues that might not be seen in text process documentation.
• Waste Reduction: Activities that do not add value, such as waiting time, overproduction, and needless duplication, are spotted by VSM, and this helps cut down unnecessary costs for organisations.
• Better Communication: These visual maps are central reference points enabling alignment between teams, stakeholders, and even departments that might be operating in silos.
• Decreased Lead Time: Streamlined workflows enable companies to reduce lead time.
• Compliance and Governance: This tool is also helpful for Compliance Officers and Audit Managers. It indicates gaps in the process to ensure alignment with regulatory standards.
VSM is an essential tool for anyone controlling a production line, managing a service team, or managing facility operations. Students and professionals pursuing operations management courses can significantly benefit from understanding and applying VSM in their work contexts.
Create a Value Stream Map in Six Steps
Now that you understand the concept and benefits of VSM, it’s time for you to create one for your organisation. Here’s a step-by-step guide:
Step 1: Define the Scope and Objective
First, identify the boundaries of the value stream you’re mapping. Is it a single process, such as customer support tickets, or does it cover the whole production cycle? Delimit your analysis by outlining the starting and end points and the problem you’re trying to address. This ensures that efforts are aligned and focused linearly.
Step 2: Gather the Right Team
Bring in all key stakeholders from the organisation to build an accurate map. For instance:
• Operations Managers are responsible for insights on workflows.
• Supervisors for concerns regarding front-line challenges.
• Compliance officers to ensure regulatory aspects are included.
Such a cross-functional team ensures many perspectives for a more robust analysis.
Step 3: Create the Current State Map
You will use actual data to outline all the steps in your selected process as they currently exist. Capture some detail elements such as:
a. Resources needed at each step.
b. Time taken for activities.
c. The information flows between each stage.
d. Existing pain points—the ones that represent delays or wastage of resources.
Use the standard symbols and shapes to represent the elements like process, material, or information flow. You can speed up this exercise through tools.
Step 4: Assess and Tap Other Non-Value Adding Activities
Analyse areas of waste typically found on your map drawn out in the current-state picture; such wastes generally appear in eight:
- Overproduction.
- Waiting.
- Excess Inventory.
- Inefficient Transport.
- Over-Processing.
- Defects and Errors.
- Unused Talent.
- Motion Waste.
These can be highlighted with kaizen bursts to mark the areas for improvement.
Step 5: Draw the Future State Map
Now, think of how the process will look in an ideal world when waste is eliminated, delays are reduced, and output quality has increased. Consider:
• Where automation might eliminate manual errors or wastage.
• Modify workflows for simplicity but without sacrificing quality.
• Whether some tasks could be combined or eliminated.
All these changes are then laid out on a future state map, a clear route map to your following actions.
Step 6: Make Changes and Assess Their Effects
Now that the future state is defined, it’s time to act and prioritise areas of most significant importance. Measure performance on key indicators such as cycle times, lead times, or throughputs to assess the effect of your changes.
Remember, VSM is a tool for continuous improvement. Occasionally refine your processes to meet new challenges and remain in top form. Understanding how to apply VSM is crucial in operations management courses and can transform organisations operation.
Conclusion:
Value Stream Mapping (VSM) is an essential and versatile tool that significantly enhances business operations and efficiency across various industries. By promoting simplicity and clarity in complex workflows, VSM enables organisations to visualise processes effectively, identify and eliminate waste, improve communication, and streamline department operations. Its structured implementation allows businesses to decrease lead times, cut unnecessary costs, and adapt to changing challenges with a continuous improvement mindset.
Incorporating principles from operations management courses, VSM can be effectively applied in various settings. In manufacturing, VSM reduces downtime; in healthcare, it improves patient flow and decreases waiting times; in facility management, it streamlines operations; and in retail and eCommerce, it smooths out bottlenecks. Applying VSM leads to better performance, cost reductions, and improved service delivery. It is an indispensable strategy for organisations committed to driving meaningful results and achieving operational excellence through the skills and knowledge gained in operations management courses.
Leave a Reply