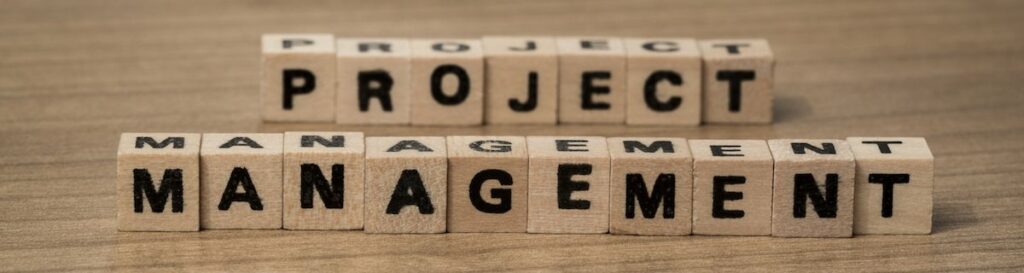
When authorisation has been given for a project to start, it is the contractor (or the main contractor, if there are several subcontractors) and the project manager who take over most of the responsibility for success or failure. Remember that the term ‘contractor’ is used here to mean not only a company that manages or undertakes a project for an external customer, but it can also apply to an internal manager or team responsible for a management change, IT or similar in-house project. Similarly, the term ‘customer’ can mean not only an external client or customer, but also the executive management of a company carrying out its own internal project.
Check out London Business Training & Consulting (LBTC)’s Project Planning and Management course.
The success of the contractor and the project manager will usually be judged according to how well they achieve the three primary objectives of cost, performance and time.
The Cost Objective
Every project should be controlled against detailed cost budgets to ensure that the expenditure authorised in its contract or charter is not exceeded. Strict attention to cost budgets and financial management is vital. A project might have to be abandoned altogether if funds run out before completion, in which case the money and effort already invested become forfeit and must be written off. In extreme circumstances over-expenditure could even cause the end of the organisation responsible.
Cost Estimation and Budgeting is covered in detail on LBTC’s Project Management courses.
The Performance (or Quality) Objective
Quality has often been used as an alternative (but less satisfactory) name for the performance project objective. General understanding of project or product quality conjures up several things in our imagination. Perceived quality characteristics will depend on the nature of the project or product, but here are a few general examples:
- performance at least equal to the specification;
- reliability and freedom from malfunction;
- long useful and economic life;
- safe: posing no unintentional threat of harm to living creatures (the adjective ‘unintentional’ is used here to accommodate, for example, projects carried out by arms manufacturers, pesticide companies and mouse trap manufacturers);
- low operating and maintenance costs;
- comfort and a pleasant impact on the human senses (sight, smell, taste, touch, hearing); and
- environmentally friendly.
In the past, quality in manufacturing and other industrial projects was seen primarily as the responsibility of a quality control department. Great reliance was placed on inspection and testing to discover faults (called non-conformances in quality management jargon), and then arranging for these faults to be rectified. In more recent years organisations in all market sectors have embraced the concept of total quality management (TQM). In TQM a ‘quality culture’ is created throughout the organisation, with quality built in to all design and work processes, and with responsibility for quality shared by all the staff and workforce from top management downwards.
Quality considerations extend well beyond industrial projects and are regarded as equally important in the service industries and other businesses. The ISO 9000 series of standards is widely accepted as the base from which to design, implement and operate an effective quality management system, with the ultimate objective of creating a quality culture throughout the organisation. The International Organisation for Standards (ISO) publishes the ISO 9000 series and a full range of other international standards (http://www.iso.org).
Check out LBTC’s Total Quality Management training courses.
The Time Objective
Actual progress has to match or beat planned progress. All significant stages of the project must finish no later than their scheduled dates. Late completion of a project will not please the project purchaser or sponsor, to say the least. Consistently failing to keep delivery promises cannot enhance the contractor’s market reputation. Further, any project that continues to use resources beyond its planned finish date can have a knock-on effect and disrupt other projects that are either in progress or waiting to follow.
A common risk to projects is failure to start work on time. Very long delays can be caused by procrastination, legal or planning difficulties, shortage of information, lack of funds or other resources and a host of other reasons. All of these factors can place a project manager in a difficult or impossible position.
All this and more is covered in extensive detail on LBTC’s Project Management Training Courses.
Leave a Reply